Welding Technology
HEAT SOURCE
CAST-DESIGNER WELD has built in a rich heat source database for different welding process, the user only needs input the heat source parameters.
- Double ellipsoid heat source
- 2D Gaussian heat source
- 3D Gaussian heat source
- 3D uniform heat source
- 3D Conical heat source
- 3D Print heat source
- Combined heat source (Double ellipsoid + 3D Conical)
- FSW heat source
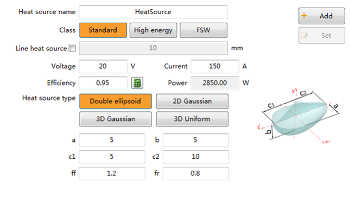
Double ellipsoid heat source
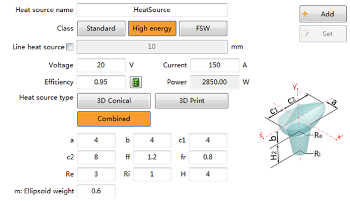
Combined heat source
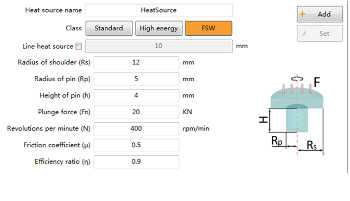
FSW heat source
LINE HEAT SOURCE
To speed up the simulation speed, the ‘line heat source’ was developed to all built in heat source. With the ‘line heat source’ option, the user can define the length of the heat source and the simulation lead time can be reduced from a few times to tens times and the result accuracy is still good enough.
Birth and Death of Elements
CAST-DESIGNER WELD used the “Birth and Death of Elements” technology to simulate the welding bead to enhance the simulation accuracy.
The numerical stability of CAST-DESIGNER WELD is unmatched, the maximum possible time step can be applied without numerical problems.
MULTI-PASS WELD DESIGN & SIMULATION
Multi Pass Welding Joints are very important part of steel construction and pressure vessel component, because defect occurs very often in them. Residual tensile stresses have negative influence on the structure lifetime and its brittle fracture resistance.
Welding sequence and intermittent welding design, which determines the best welding pattern in multi-pass welds, are familiar techniques to control the distortion when dealing with multi-pass welded structures.
Finding the best solution for such a design is limited by available resources since a designer needs to pick one out of many patterns i.e. hundreds to thousands of patterns, usually based on experience.
Optimization of this problem is not feasible through shop trials, so we use computer modeling that automates the implementation of several patterns for minimal distortion, residual stress, or other design objectives. Using this signature technique based on surrogate modeling we can efficiently select the best pattern out of tens of thousands of the pattern or all possible weld sequence configurations.
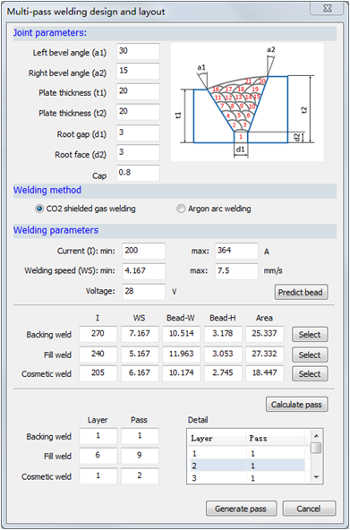
Multi-pass weld layout design
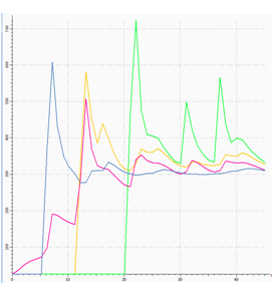
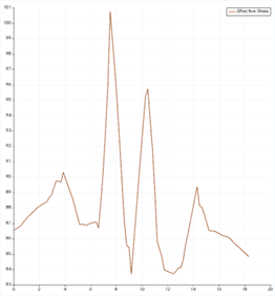
Temperature vs time (up) and residual stress vs point (down) distribution curve
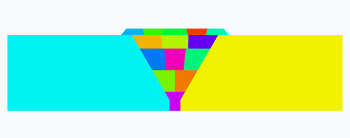
Designed multi-pass layout
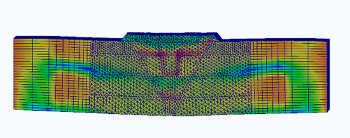
Mesh, residual stress and distortion
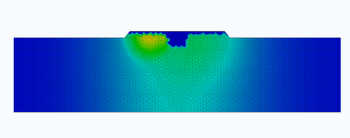
Temperature distribution during weld
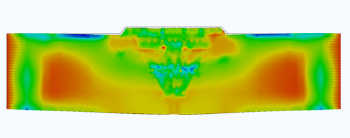
Residual stress after welding
JOINT DATABASE
A Joint Database for MAG/MIG steel, laser welds and aluminum are provided in CAST-DESIGNER WELD. It includes more than 30 welding joint types. The database can be adapted and extended by the user with new joint types for special applications.
One application of the joint database is used for calibration of heat transfer into the structure in a welding or assembly simulation. Welding joint can be assumed that can be manufactured under valid process conditions, as for example described in the American, European, Japanese or Chinese normal.
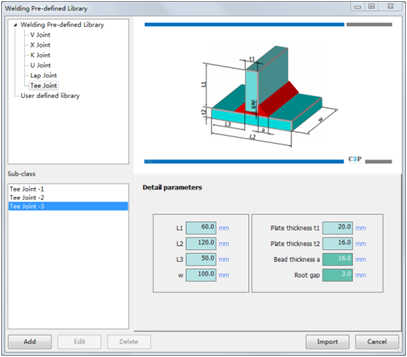
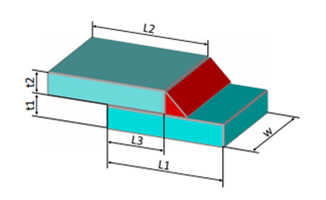
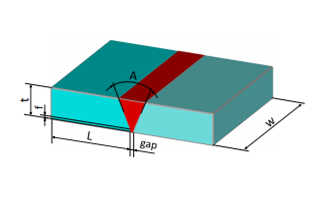
Joint database
WELD POOL SIMULATION
The accurate simulation of transient temperature distributions in the part needs to carefully take account of the fluid flow in the weld pool. Usually surface tension effects (including both the “curvature effect” and the “Marangoni effect”), buoyancy forces and free surface motion should be token account.
It is important to capture all the relevant physical phenomena to have a realistic process simulation.
The CAST-DESIGNER WELD CFD solver can provide very detail result of the weld pool with all build in heat source.
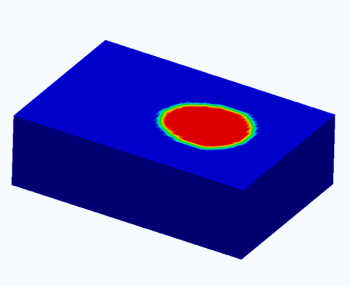
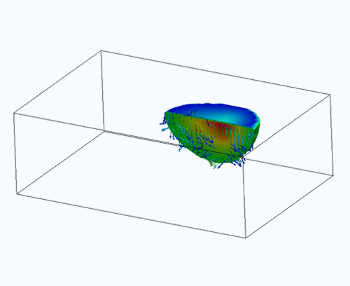
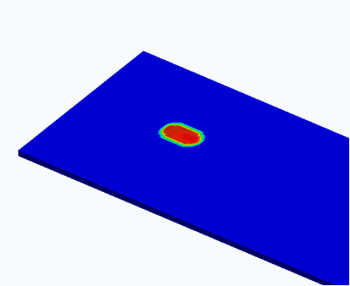
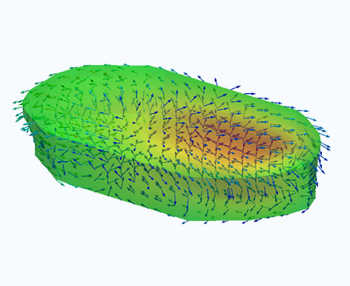
Weld pool simulation (Temperature and velocity of the pool)
PARALLEL COMPUTING
Both the CAST-DESIGNER WELD CFD solver and FEM solver can run jobs in parallel processing. The Cast-Designer DMP solution (Distributed Memory Parallel) uses the latest available technology, in particular dynamic domain decomposition and message passing communication.