Smart Assembly
The Smart Assembly is a key product to simulate the metal welding and assembly process in the Cast-Designer Weld software package. It is using a fast thermo-mechanical couple simulation method for the assembly distortion prediction. The advantage of Smart Assembly is it can handle big and complex model and easy to use, also the simulation result was very robust.
- Use Lagrange FEM method, with long time validation.
- Detail welding parameters and speak industrial language
- Easy to use and short learning curve
- Study welding sequence
- Flexible boundary condition
- Fast modeling and fast simulation
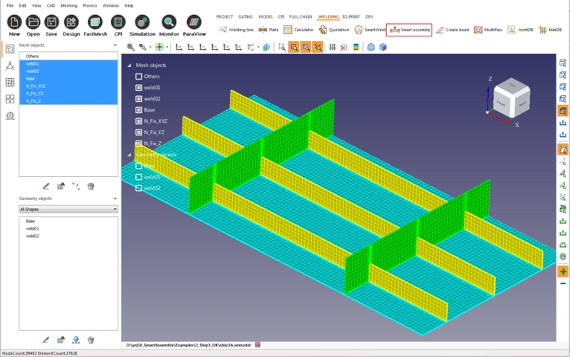
Smart Assembly's Simulation Approach
General method: The Inherent Strain Method
The elastic FE simulation with inherent strain or the inherent deformation method is the most successful method for predicting welding distortion in large and complex welded structures. The inherent strain method was proposed by Ueda to measure residual stress initially and then has been widely used to predict deformation.
Advantage:
- Fast simulation
Disadvantage:
- Use Lagrange FEM method, with long time validation.
- Detail welding parameters and speak industrial language
- Easy to use and short learning curve
- Study welding sequence
- Flexible boundary condition
- Fast modeling and fast simulation
Smart Assembly's Simulation Approach
The Smart Assembly uses another approach to apply the thermal load to the structure:
- Calculate the thermal distribution based on the parameters of the welding process. i.e welding current, Voltage and welding speed
- Based on the thermal-mechanical relationship, to calculate the inherent stress from the thermal load
- The welding sequence and related parameters of each welding line could be considered together or one by one
No local-global model required and more accurate result
Easy to model setup, widely welding process
Weld Line & Layout Design
- Special tools was designed for the weld line and bead layout.
- Free draft style, mouse click operation
- Smart snap CAD edge and continue the weld line automatically
- Input design plan in CSV file format (external design plan)
- Input design plan in DXF file from AutoCAD or other CAD system
- Flexible manage tools for the designed weld bead
- Save design to template file
- Multi-design plans comparison
- Generate CAD wire from design bead
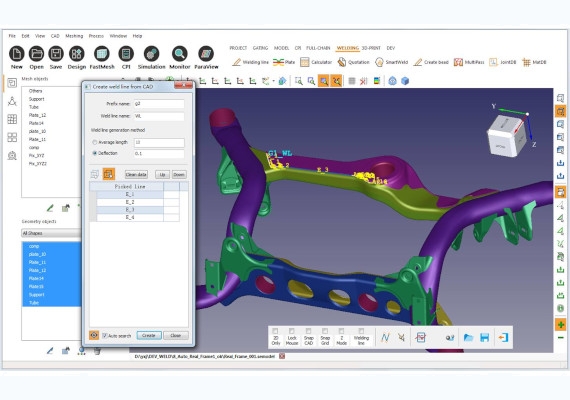

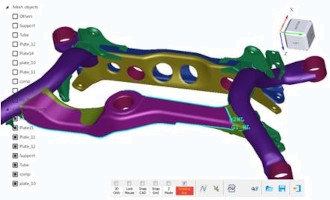
FastMesh: Unique Mesh Technology
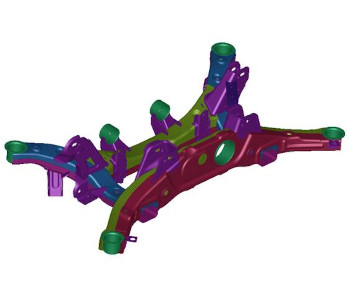
CAD
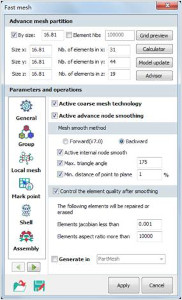
Fast Mesh
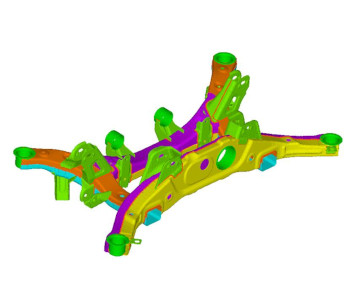
Mesh
Fully automatically mesh generation
Very strong 3D hexahedron and tetrahedron mesh capability for complex geometry
Support GUI mode and batch mesh mode, fully parametric, easy to re-mesh.
Special treatment for CAD defects, i.e. geometry gap, overlay, intersection or unclose, face lose etc.
Rich mesh options: local mesh, mark point, tin region mesh, 2D surface mesh, shell mesh, advance mesh smoothing, quality control etc.
Fully automatic mesh assembly, support mixture mesh type.
Bar element as weld line.