ParaCAD for Die Face Design
PARACAD OVERVIEW
Instead of the standard CAD interactive operation, the AI-FORM requires the CAD operation in the batch mode, so that the optimization engine can drive the CAD creation and modification.
Once the part geometry is available, the predefined standardized process guides the user from part preparation for binder design, then addendum design and die face generation. More ever, many standard CAD functions are built in the ParaCAD for a general parametric design environment; it can be used to design any geometrical shape not only the stamping die surface.
ParaCAD is the result of an innovative, unique and quality-oriented approach in process design which improves and facilitates daily work in tool design departments.
Customer Benefits
- Easy and rapid creation of high-quality CAD surfaces.
- The customizable standard approach to process design including all operation types.
- A consistent methodology for CAD quality die face design.
- Significantly enhanced productivity.
Main Features
- Fill the hole and multi-hole filler, rounded extend.
- Automatic tipping and Auto-Binder generation.
- Rapid create addendum and binder surface trimming.
- Easy-to-use dedicated surfacing tools with built-in analysis features.
- Specially designed features for process designers such as PAL and DOL, trim line, drawbead, etc.
- Automatic update functions.
- Support for company-wide workflow standardization and data consistency.
It’s Like Drawing on a Paper
Working in 'Free-Style' die face design module is fun and easy & get your design done in minutes.
- Use the tipping tool to tip the part to a proper draw position. Three criteria are available to tip the part: minimum undercut, minimum drawing depth and maximum contact area.
- Hide or unfold flanges while taking into consideration material thickness and natural surface ratio. Do it efficiently while saving time and avoiding errors.
- Automatically close small and large holes on a part surface. Also, extend surfaces tangent to part for smoother definition of the hole fills.
- Rapidly create accurate and high-quality Binder Surfaces. Easily modify Binder surfaces to adapt the part shape or independent shapes.
- Define the PAL & DOL, which will guide the addendum design and associate to the trim binder face also.
- The system provides rich tools to create the addendum profile, no limitation to the profile shape and parameters. The pre-defined template is also included.
- Create Fast and Accurate Addendums from the defined profile to adapt the part and binder. Several surface methods were provided.
- Trim the binder and get the final die face in full CAD format.
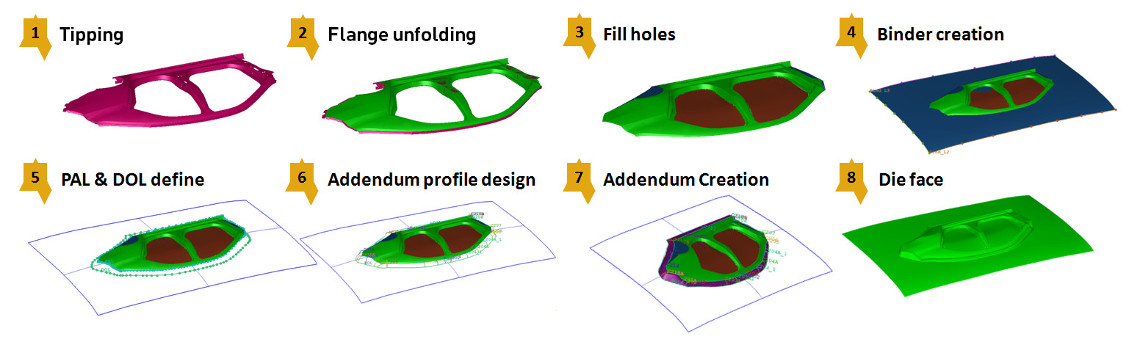
Since all surfaces and profiles are parametrically defined; the binder surface, addendum profiles/surface, and DOL line are also fully associated. Therefore, modification of one entity can be extended to the other objects due to the associative characteristics.
The geometry of the drawbead has a great deal of influence on the accuracy of the springback results. Within ParaCAD, the commonly used drawbead geometry can be parametrically generated and interchanged with the line drawbead.