DFM: Part Base Analysis
The DFM (Design for Manufacturing) analysis is the first step for part manufacturing. DFM is the bridge to link the part designer and manufacturing suppliers. Geo-Designer is a powerful Upfront DFM tools for designers and manufacturing engineers with innovative technology. It accelerates the design process for functions, manufacturability, enabling designs to move to production better and faster. If we compared Geo-Designer with other traditional tools, it is found that the Geo - Designer is powerful, flexible, fast and easy to use and provides savings in downstream costs of quality improvement in the design stage.
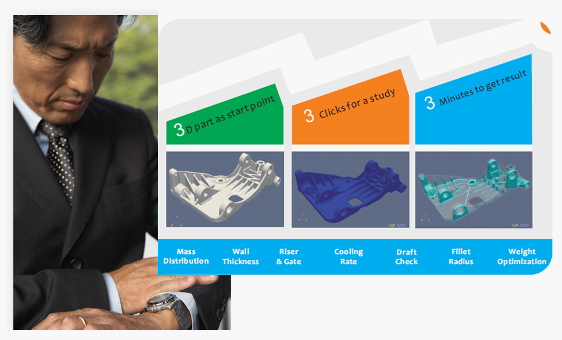
Geo-Designer can bring a very clear benefit to casting part designer and mold supplier, such as MDI(Mass Distribution Index) /HDI (Heat Distribution Index) analysis, slider checking, draft angle and undercut checking, ejection force evaluation, riser and feeder design, cores extraction, cooling system designer, etc.
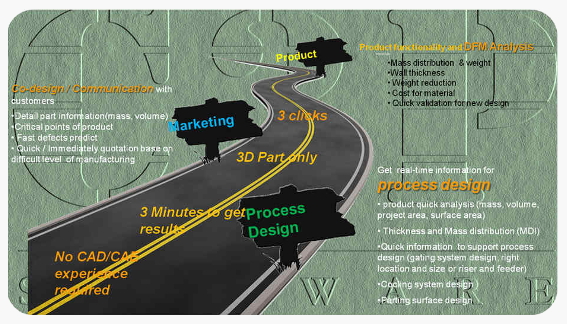
Geo-Designer can be used for both OEM and supplier companies. With Geo-Designer, the product designer, supplier marketing engineer and process designer could make synchronous design together.
DFM Analysis for Casting Part
Geo-Designer offers a new method to study the part geometry in 3D iso-surface mode with flexible transparency. It is similar to the x-ray and CT method in the industry. Geo-Designer has introduced MDI (Mass Distribution Index) and HDI (Heat Distribution Index) for part analysis and evaluation.
MDI Checking
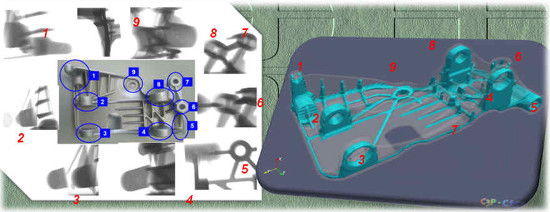
The MDI (Mass Distribution Index) can be used to check the heavy mass distribution of the casting part, where it is easy to cause the hot spot and shrinkage porosity during the casting process. As a product design engineer, you should try to avoid big MDI on the part.
During the manufacturing phase, the MDI result can be used directly for inner gate design, riser and feeder design, cooling channel layout and hot spot prediction.
Slider checking
For die casting and permanent mold casting, the slider number and complex level are an important factor of the die set cost. Geo-Designer can perform slider checking for casting part to help slider design. Simply define the plug direction or opening direction and the partition plan, then the system will calculate the others. More ever, the surface of ‘Slider Zone’ can be also exported to CAD system in STL file format to guide the slider design in 3D CAD system.
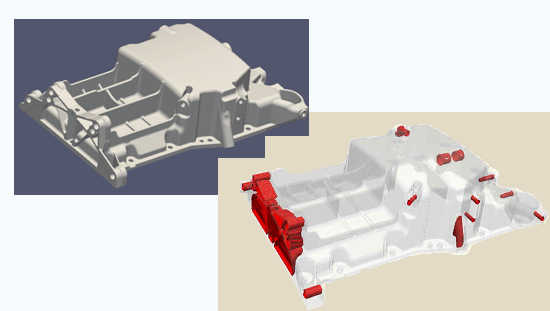
Evaluate the design plan of casting system
The MDI information can also guide the gating system design. For example, the following part is used for a communication device, due to the heavy MDI on the contact shaft, gas entrapment and shrinkage porosity will be existed there, and the gas escapement will break the coating layer in sliver after a couple of months and damage the whole system. The first gating was complex, but cannot solve the gas problem and shrinkage problem, the part yield ratio was only 67.1%. After checking the MDI in Geo-Designer and understanding well of the geometry of the part, then changed the gating system to the later one, and using the 3rd phase pressure to reduce the shrinkage porosity, then the yield ratio of the part has been increased to 92%.
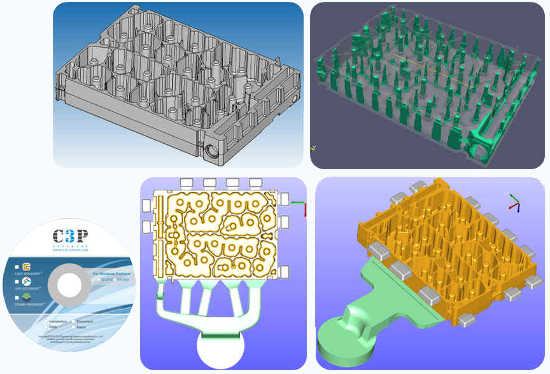
Other analysis functions
The other functions could be provided by Geo-Designer for part analysis, such as
- Ejection force distribution and evaluations
- Draft angle checking and undercut checking
- Fillet radius checking
- Thin wall thickness checking
- General part information, such as mass, volume, project area and thermal modulus
To Assist Gravity Casting Design
Riser & Feeder design
The powerful HDI analysis of Geo-Designer can help the riser, feeder, insulator sleeve and chill design, specially used for gravity casting. If we compared with other experience formulas and graphic programs, the Geo-Designer approach is more flexible, accurate and easy to use. Since all the experience formulas are very difficult to consider in the 3D geometry, it is usually quite complex.
In HDI calculation, the system will also consider the heat affection of the around media. For example, heat affection by the feeder or riser. It is also possible to consider the different material type, such as the chill to speed up cooling, the insulators to keep the heat and cool down slowly.
Based on the HDI results, the user can design riser and feeder on the thicker zone to compensate the metal shrinkage. The online checking result was very clear, both the component size and location could be designed well by the assistant of the Geo-Designer. More ever, the updated HDI/MDI result can be obtained immediately, just click a button, anything has been updated. So, it is hundreds of times faster than the numerical simulation method. The final design result can be exported to Cast-Designer system or other CAD system in STEP file format.
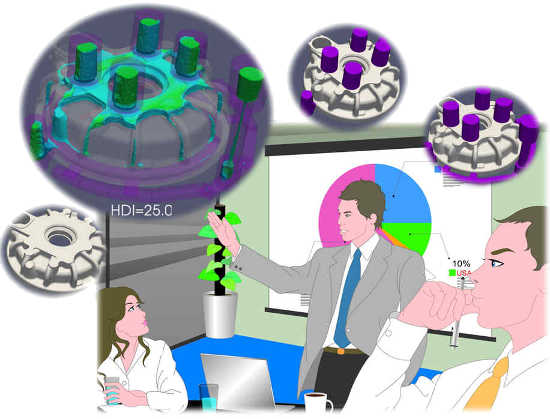
Core design and checking
For complex casting part, such as the engine block, the designer must consider the sand core inside the part, this is very important and with big challenge. The section area and geometry shape of the core must be designed carefully.
With powerful Boolean operation function in mesh base, the Geo-Designer can extract the inner core from the existed casting part easily. Then, the user can analysis the detail sections of the core or export the core surface to another system in STL file format.
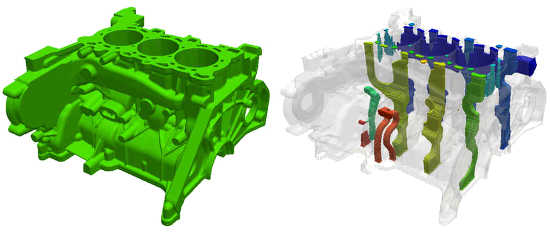